FODS Trackout Control System Featured in Grading and Excavation Contractor Magazine
FODS Trackout Control System for stabilized construction entrance was featured in the February issue of Grading & Excavation Contractor magazine. Read more... Project Profile: Rock and Rails

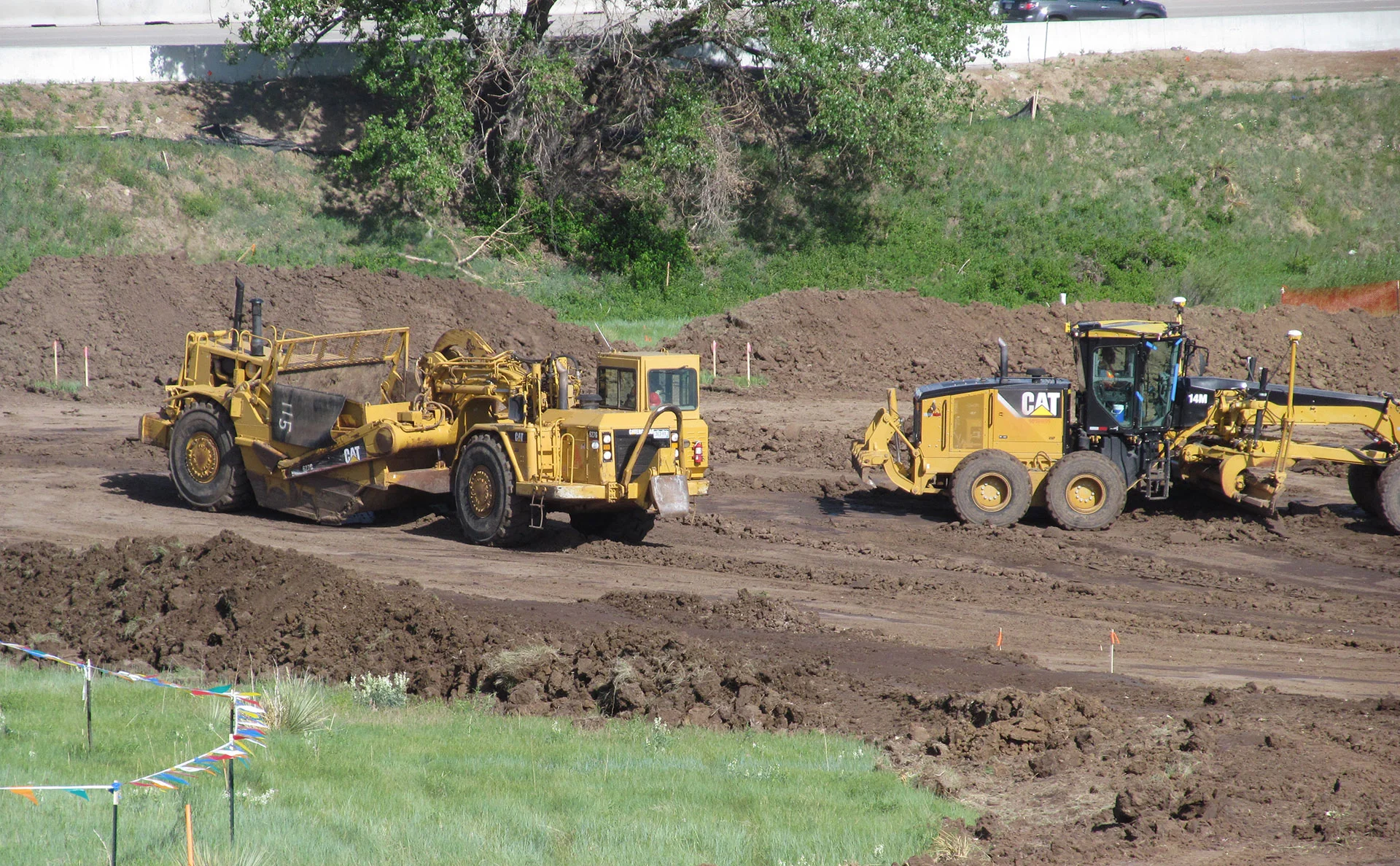

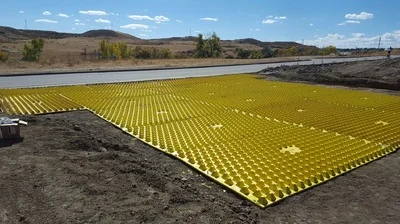



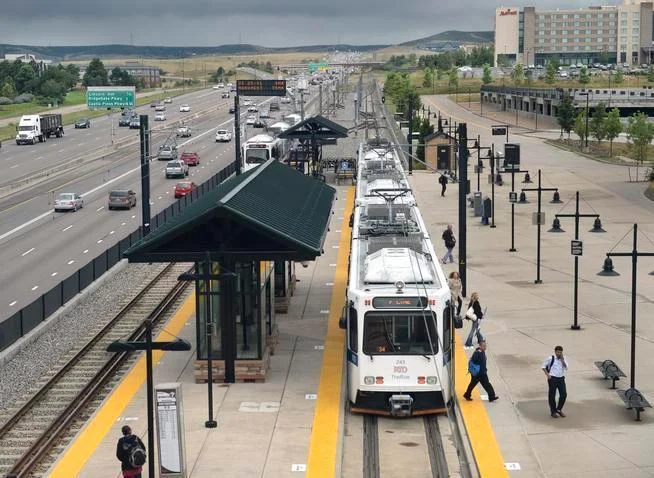
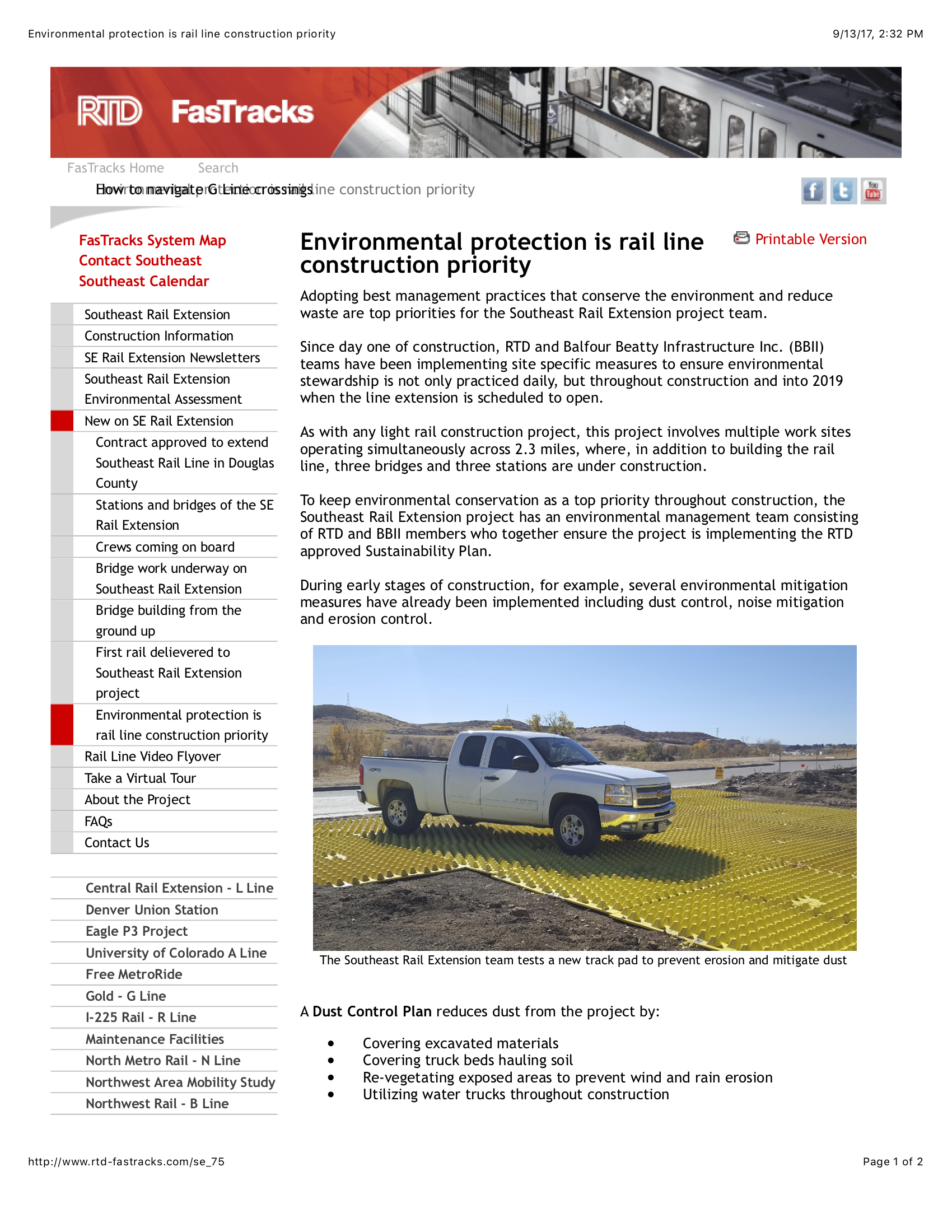
In 2004, Colorado voters approved a multi-billion-dollar public transportation expansion called FasTracks. Developed by the Regional Transportation District (RTD), the plan consists of new commuter rail, light rail, and express bus services. The ambitious plan called for building six new light rail lines consisting of both electric commuter rail and diesel-powered rail lines. In total, the project delivers a combined 122 miles of rail lines.
As a government entity that works with multiple cities and municipalities across Colorado, RTD is always looking to uphold its responsibility to operate environmentally friendly and safe construction sites. For this reason, RTD looks to Best Management Practices (BMPs) that conserve the environment and reduce waste.
Annually, RTD will select a project on which to test newly innovated BMPs. For 2017, RTD selected the Southeast Rail Line Extension. Located south of Denver in Lone Tree, CO, and operated by Balfour Beatty Construction, the Southeast Rail Line Extension construction project is a $223.6 million portion of the FasTrack program that connects 2.3 miles of new light rail line to the city of Lone Tree to 19 miles of existing rail line, which runs from downtown Denver to the rapidly growing south metro area.
The Southeast Rail Line Extension consists of multiple construction sites operating simultaneously along the 2.3-mile rail line extension. As with all of their construction sites, RTD and Balfour Beatty wanted to ensure that they were practicing proper environmental stewardship.
In the early stages of construction, the environmental management team focused on three main areas of environmental concern: dust control, noise mitigation, and erosion control—the most important BMPs. Of these environment measures, the Lone Tree site inspector, Ward Mahanke, noted that erosion control issues in the form of construction site trackout are the most common concern that he experiences on nearly every project in the city.
Construction site trackout of mud, dirt, and other debris causes both environmental concerns of mud entering the stormwater system and a safety concern from mud and rocks being deposited on public roads.
In an effort to address the site trackout and to mitigate the dust from the job site, the team from RTD and Balfour Beatty installed a FODS composite mat trackout control system. The system is installed using 12- by 7-foot long mats linked together to create a uniform composite trackout control system.
Composite trackout mats offer multiple advantages compared to traditional rock stabilized construction entrances. Unlike traditional construction site entrances installed using geo-synthetic fabric and rocks, composite trackout mats like FODS don’t lose their effectiveness when the aggregate is tamped down and embedded in the earth from extremely heavy vehicles driving across the entrance.
Bryce Clingerman, Chief Operating Officer at FODS, points out, “What makes FODS mats so different is that the pyramids are always working whether one vehicle or 10,000 vehicles have driven across the entrance—FODS is still removing dirt and cleaning tires.” Since the pyramids do not flatten when vehicles cross over them, they are much more effective at removing mud than traditional rock. The strong structure of the pyramid gets inside the lugs, which increases the effectiveness of the system to remove debris from tires.
One of RTD’s particular concerns was the dust that arises from traditional trackouts that allow mud and dirt to build up on their surface as the rocks become tamped down. Once the built-up mud dries, vehicles create dust as they pass over the entrance.
The focus on dust control led Balfour Beatty and RTD to note one of the advantages of FODS trackout mat. Due to the patented staggered pyramid design of the control mats, the system cleans the entirety of each tire, forcing open the lugs, causing mud and dirt to fall out. Once the mud is removed from the tires, it falls to the pan or base of the mat where it is undisturbed by vehicles moving across the top of the pyramids on the mats. The vehicles ride on the top inch of the pyramids. Therefore, the tires do not come in contact with dirt that had been deposited previously. This greatly reduces the amount of dust that is associated with typical construction site trackout as the dirt is left undisturbed.
An additional advantage offered by composite trackout control mats is that they do not contain any rocks. By installing a trackout system, RTD eliminated the concern of rocks becoming trapped in the lugs of tires or between the dual wheels on the rear axle of large trucks. These rocks become projectiles once the vehicles reach high speed after entering the public roads. This issue is well-documented for causing damage to vehicles and injury or even death to drivers, passengers, or pedestrians. The rocks also get onto sidewalks making an imposing hazard to pedestrians, wheelchairs, bicycles, and other non-motorized sidewalk users.
FOD’s trackout control mats are designed to last 12–15 years. This allows RTD to reuse the mats by relocating the track-out system as the project moves down the rail line. The mats used by RTD and Balfour Beatty were taken at the conclusion of the project and are currently in use on a different construction project in Colorado.
During the BMP field trial, RTD found that through the incorporation of multiple innovative BMPs, the team was able to achieve its goal of eliminating job site trackout onto public streets, greatly reducing the amount of dust created, and mitigating the amount of noise created during construction.